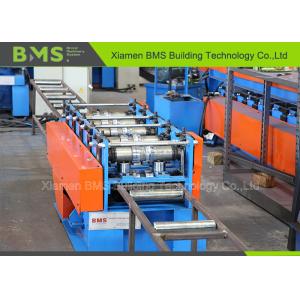
Add to Cart
Motor Driving Shelf Occlusion Machine 5.5KW Power PLC Automation Control
Product parameters:
1. Forming pass: 5 sets of roll forming (upper and lower are a group)
2. Roll material: national standard Cr12 mold steel
3. Heat treatment: All the roll molds have been heat-treated to a hardness of HRC = 58-60º (refined after treatment)
4. Spindle material: 45 # steel, quenched and tempered
5. Frame structure: A3 board integral welding thickness 18mm
6. Transmission mode: chain transmission, all chain sprocket are processed by high frequency
7. Transmission power: 5.5kw Polaroid K series or R series
8. Frame structure: square tube integral welding
9. Cutting method: hydraulic automatic cutting
Random accessories: a set of feeding rack, an operation cabinet, two sets of operating procedures and instructions
Forming part: The roll forming system is composed of a frame, a transmission part, and a cold-formed roll set. It is divided into precision-molded wheel rotation molding, which has a good molding effect, reduces the friction between the wheel and the raw materials, and is easy and fast to debug.
Workflow: uncoiler--guided feeding--roll forming--fixed-length cutting--finished product out of the sheet
Enter the PLC operation page-press the "Start" button-the board automatically enters-start according to the set program-it will automatically cut off after reaching the set size. The roller forming is completed.
Feeding guide platform: Left and right guide devices are set at the main machine's feed inlet. During work, the two sides of the raw material sheet are guided into the host through left and right, so that the raw material sheet and the roll forming system maintain the correct position. The guide position can be adjusted by the manual screw mechanism and left and right can be adjusted independently.
Cutting system after molding: The cutting system consists of a cutting frame, a cutting mold, a guide device, and a cutting cylinder. The cutting knife material is precision turning and heat treatment.
Electric control system: It adopts Schneider PLC control, frequency conversion and speed regulation, which can realize the whole machine automatic production. Can set batch, workpiece length, quantity, etc.
Operation method: Touch screen + Button. Encoder counting(Omron), with counting and counting function.
Hydraulic system: using the external independent hydraulic station (to provide power for cutting off)
Parameter table | Item | Unit | Parameter | Remark |
1 | Raw material | Coil or sheet | Q235 1.0-2.5mm | |
2 | Profile width | |||
3 | Production speed | m/min | 20 | |
4 | Roller material | National standard Cr12 mold steel | ||
5 | Driving mode | External motor drive | ||
6 | Operating procedure | Touch screen | ||
7 | Total motor power | KW | About 5.5 | |
8 | Control system | Set | PLC automation control |